AMF Enterprises
Top Errors to Avoid When Maintaining Your Truck's DPF System
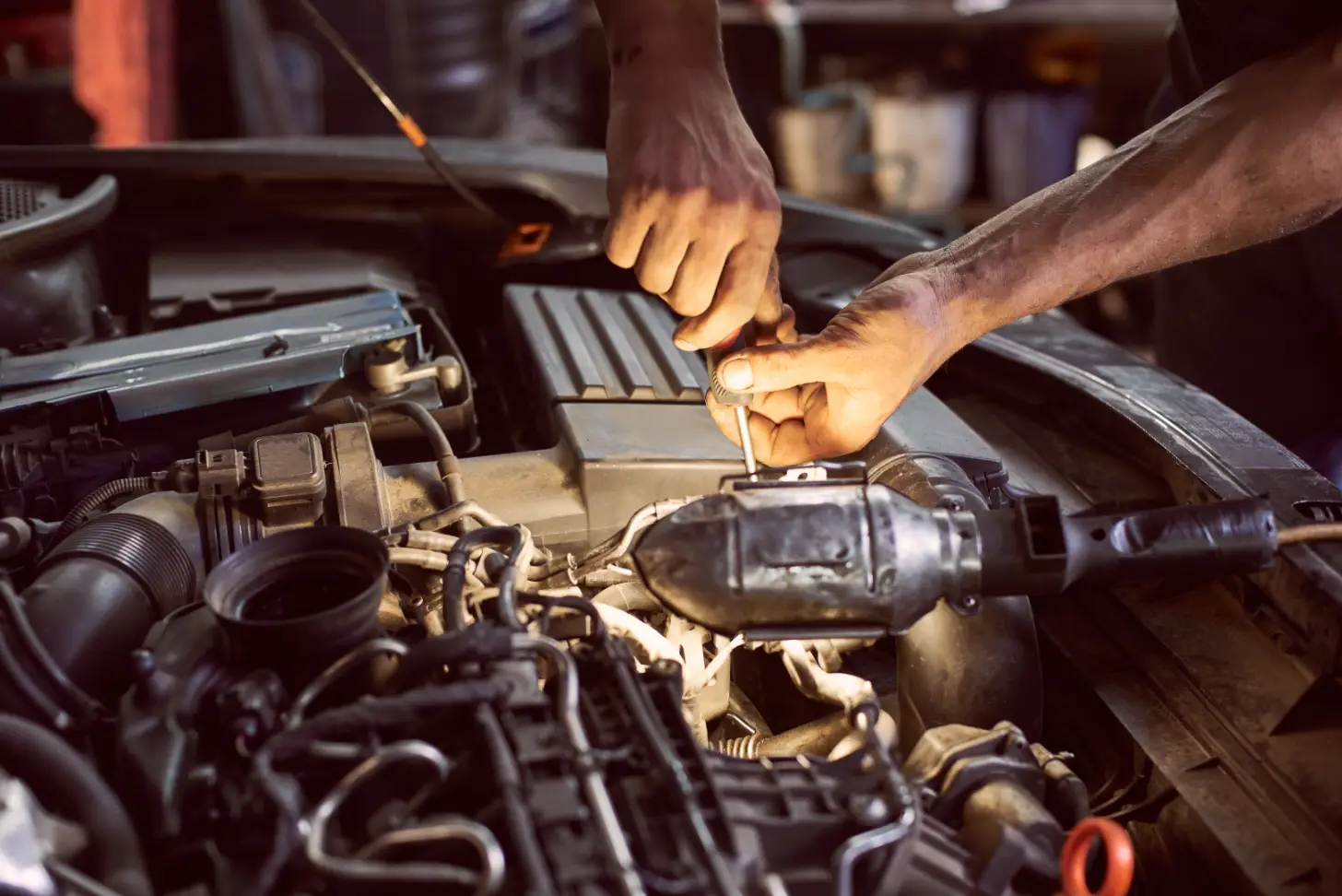
Introduction
A Diesel Particulate Filter (DPF) is one of the most critical emissions control components in modern diesel trucks. Designed to trap and remove soot from the exhaust system, the DPF helps reduce harmful emissions and keeps trucks compliant with EPA and DOT regulations. However, when improperly maintained, the DPF can become clogged, leading to engine power loss, poor fuel economy, and expensive repairs.
Many truck owners unknowingly make critical mistakes when maintaining their DPF systems, resulting in unnecessary breakdowns, costly replacements, and even out-of-service violations. Understanding these errors and how to avoid them ensures longer filter life, lower maintenance costs, and improved overall performance.
How the DPF System Works
The DPF traps particulate matter (soot) from diesel exhaust and burns it off through a process called regeneration. Regeneration occurs in three ways:
- Passive regeneration happens naturally when exhaust temperatures are high enough to burn off accumulated soot.
- Active regeneration is initiated by the engine’s ECM, injecting fuel into the exhaust stream to increase temperatures and burn off soot.
- Forced regeneration is a manual process performed using a diagnostic tool when the DPF becomes too clogged for passive or active regeneration to work.
If the regeneration process is interrupted or ignored, soot builds up in the filter, causing excessive backpressure, engine inefficiency, and potential DPF failure.
1. Ignoring DPF Warning Lights
One of the most common mistakes truck owners make is ignoring the DPF warning light on the dashboard. This warning indicates that the filter is clogged and requires regeneration. If left unaddressed, the ECM may trigger a limp mode, reducing power and speed to protect the engine.
Once the warning light appears, drivers should allow the truck to complete a regeneration cycle. If the light persists after regeneration, the filter may be too clogged and require a manual forced regeneration or professional cleaning.
2. Frequently Interrupting Regeneration Cycles
Regeneration cycles need uninterrupted time to complete. Many drivers shut off their engines mid-cycle, preventing the DPF from burning off accumulated soot. Over time, this leads to excessive soot buildup, forcing more frequent regenerations and potential filter failure.
To avoid this, drivers should allow the regeneration process to finish completely before turning off the truck. If the DPF light is on, it’s best to continue driving at highway speeds to allow the system to reach the necessary temperatures for a full burn-off.
3. Using the Wrong Type of Engine Oil
Not all engine oils are compatible with DPF-equipped trucks. High-ash content oils contribute to filter clogging because the additives do not burn off completely during combustion. This results in excessive residue buildup inside the DPF, shortening its lifespan.
Always use low-ash, DPF-friendly oil that meets API CK-4 or FA-4 specifications to ensure optimal engine and emissions system performance.
4. Neglecting Regular DPF Cleaning
The DPF is a wear item that requires periodic cleaning to function efficiently. Some truck owners wait until the filter is completely clogged before servicing it, leading to increased backpressure, reduced fuel efficiency, and engine damage.
A professional DPF cleaning service every 100,000 to 200,000 miles helps remove excess ash buildup, restoring the filter’s performance. Fleet operators should also consider regular filter inspections to detect early signs of clogging.
5. Deleting the DPF System
Some truck owners attempt to bypass DPF maintenance by deleting the system entirely. While this may seem like a way to improve fuel efficiency and reduce maintenance costs, it is illegal in the U.S. and Canada under EPA emissions regulations.
Removing the DPF system can result in hefty fines, loss of registration, and failed DOT inspections. It also voids warranties and makes the truck non-compliant for commercial use. Instead of deleting the DPF, proper maintenance ensures regulatory compliance and long-term reliability.
6. Running Low-Quality Diesel Fuel
Using low-quality diesel with high sulfur content increases soot production, causing the DPF to clog more quickly. Some fuels also contain excessive biodiesel, which burns at lower temperatures, producing more soot and deposits inside the filter.
To minimize DPF clogging, always use ultra-low sulfur diesel (ULSD) and high-quality fuel additives that help maintain cleaner combustion.
7. Ignoring Exhaust Leaks
Exhaust leaks before the DPF can cause incorrect sensor readings, leading to poor regeneration cycles and premature filter clogging. Even a small leak in the exhaust system allows cooler air to enter, lowering exhaust temperatures and preventing the DPF from reaching regeneration conditions.
Regular inspections of exhaust pipes, turbo connections, and gaskets help detect leaks before they cause major issues. Fixing leaks promptly ensures that DPF regeneration operates as designed.
8. Overusing Manual Forced Regeneration
Forced regeneration is a temporary fix for a clogged DPF and should not be relied on as a regular maintenance strategy. Excessive forced regens can cause thermal stress on the DPF, reducing its lifespan and increasing the risk of cracks or internal damage.
If a truck requires frequent forced regens, it’s a sign that there is an underlying issue, such as low-quality fuel, engine misfires, or clogged EGR valves. Diagnosing and resolving the root cause prevents excessive soot buildup.
9. Neglecting EGR System Maintenance
The Exhaust Gas Recirculation (EGR) system works alongside the DPF to reduce emissions by recirculating a portion of exhaust gases back into the engine. A failing EGR valve can cause higher soot production, leading to faster DPF clogging.
Regular EGR system inspections, cleaning, and valve replacements help prevent excessive soot buildup and extend DPF service intervals.
10. Skipping Diagnostic Scans
Modern diesel trucks have advanced onboard diagnostics (OBD) that monitor DPF efficiency, soot levels, and regeneration cycles. Ignoring check engine lights or diagnostic trouble codes (DTCs) can lead to undetected issues that worsen over time.
Performing regular diagnostic scans helps fleet managers catch minor DPF issues before they turn into expensive repairs. Addressing error codes early prevents unexpected breakdowns and DOT compliance failures.
Best Practices for Proper DPF Maintenance
To maximize DPF lifespan and reduce unexpected failures, follow these best practices:
- Drive at highway speeds regularly to allow for natural regeneration.
- Avoid excessive idling, which increases soot buildup.
- Use high-quality diesel fuel and low-ash engine oil to reduce filter clogging.
- Perform regular DPF cleaning to remove excess ash.
- Inspect the EGR and turbo system to ensure they’re functioning properly.
- Monitor dashboard warning lights and act quickly when issues arise.
Conclusion
Maintaining a healthy DPF system is essential for engine performance, fuel efficiency, and emissions compliance. Avoiding common mistakes like ignoring warning lights, interrupting regens, using the wrong oil, and neglecting regular cleaning ensures longer filter life and fewer costly repairs.
By following a structured DPF maintenance plan, truckers and fleet operators can reduce downtime, improve fuel economy, and avoid regulatory penalties.
For professional DPF cleaning, diagnostics, and emissions system repairs in Summersville, WV, contact AMF Enterprises today.